When you drink a refreshing glass of water, do you think about where that water came from? If you’re drinking from a well in Missouri, you might have Flynn Drilling Company to thank.
Since Mike Flynn Sr. founded the company in 1954, Flynn Drilling has been providing complete water services throughout the state. The Flynn family – first Mike Sr., then his wife Katy, now their son Danny – has run a tight ship since the beginning. Their objective: 100% customer satisfaction.
Of course, 100% customer satisfaction wasn’t easy in 1954 and it’s not easy today. To provide a great experience, you need consistent results. To produce consistent results, you need employees who are happy, healthy, and confident on the job.
Workplace culture matters
Fostering this high-achieving culture is something Flynn Drilling does very well. “We have very little turnover,” explained Kurt Harke, Chief Operations Officer. “Many of our guys have been here ten to twenty years.” That kind of loyalty isn’t common, especially in their industry. Higher-risk industries like construction and utilities see annual turnover as high as 50-60%.
What’s their secret? “They hire the right people, and they treat them well,” said Kevin Flynn, the company’s insurance agent and – you guessed it – Danny Flynn’s brother. However, it takes some effort to look past the drilling industry’s overall risk profile and see this company’s culture of excellence. In the early days, that wasn’t something Flynn Drilling’s insurance carrier was willing to do.
Kevin explained: “Before we moved them to a policy with Missouri Employers Mutual, it was hard to find a carrier because of their high-risk industry.” When MEM was founded in 1995, Flynn Drilling became one of our first policyholders.
A few years into the partnership, however, the company had three major claims in one year. “It was an anomaly, and I advocated for MEM to keep them despite the setback,” Kevin recalled. If MEM canceled the policy, they would have likely gone to the pool, or the state-assigned plan for businesses unable to get coverage from a standard carrier.
“If they’d been sent to the pool, they wouldn’t have gotten the safety services they needed to get back on their feet,” Kevin explained. “MEM believed in them. Part of their success in terms of safety has been MEM.”
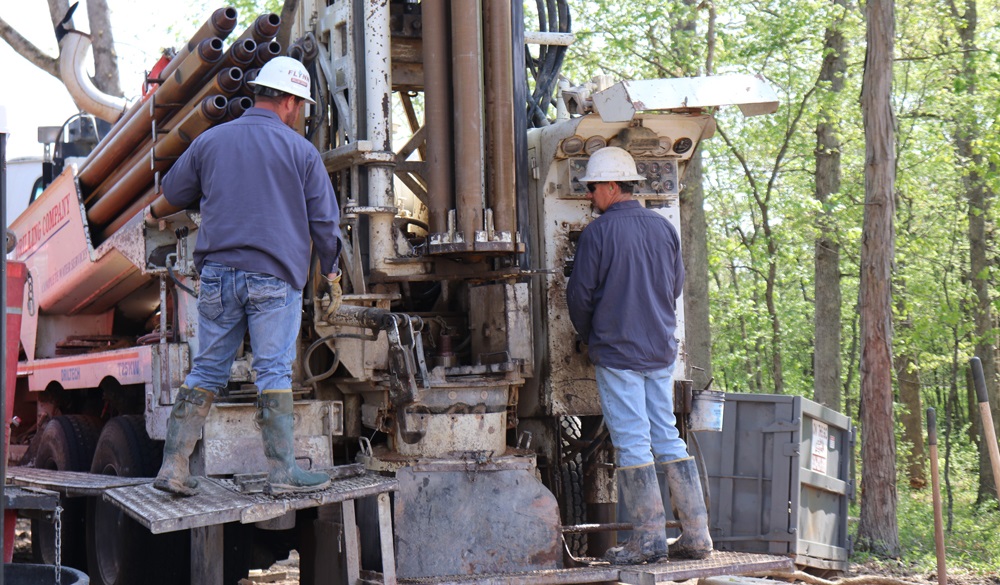
Industry leader in safety
Today, nearly 20 years later, Flynn Drilling joins us in celebrating our 25th anniversary as one of our oldest policyholders. Their safety record is miles above the industry average. The company has about 50 employees, most of whom work on location at job sites, installing and servicing water wells. Employees typically work in small teams. They change job sites as frequently as every few days – or even hours. In this dynamic and dispersed work environment, company leadership must work hard to keep safety top of mind for everyone.
“We have safety meetings with all employees on the first Monday of every month,” explained Harke. At the meeting, Danny covers a focused topic with the group. Then, he opens the floor for employees to share their own experiences related to the topic, including near misses. You might think employees would be hesitant to share these stories, but Flynn Drilling’s culture provides a safe place to discuss them. “The employees take it as a learning opportunity. If we can prevent a future injury, it’s worth talking about,” Harke said.
Crews also head out to their job sites equipped with Tool Box Talks, safety checklists and other physical resources that they can reference every day before beginning work.
Safety grant prevents electrical shocks
Some common safety topics for Flynn Drilling: hard hat use, personal protective equipment policies, and electrical safety. Last year, the company was selected to receive an MEM safety grant to purchase arc flash safety suits. These protect employees from shocks while working with the electrical components on a well, which can carry high voltage on a municipal job. Employees also follow stringent protocol when working around electricity to ensure they take all the necessary precautions.
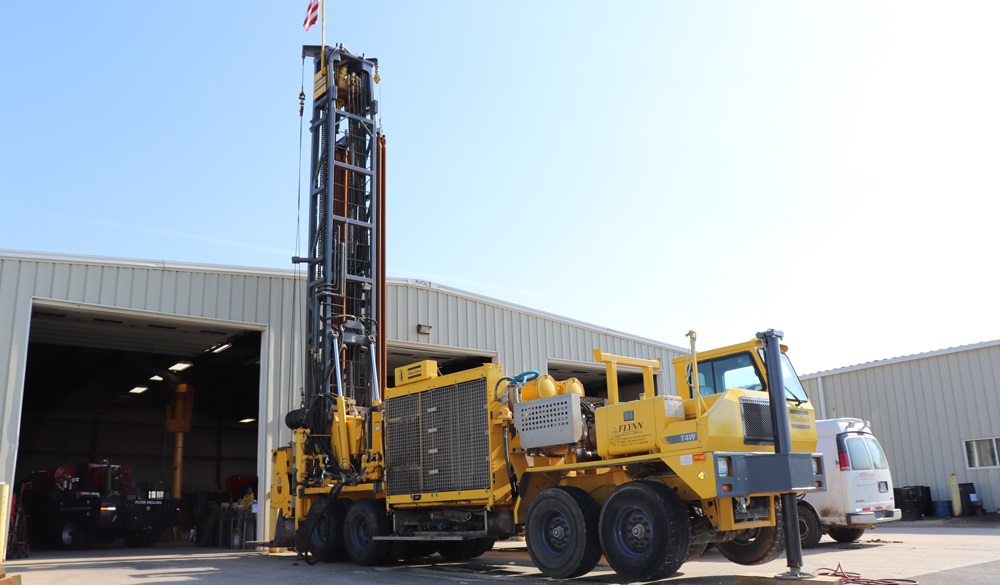
Resident mechanics provide proactive maintenance
At MEM, we talk a lot about return on safety – that is, the return you get on an investment in safety resources, equipment or other improvements. A few years ago, after decades of outsourcing maintenance on their heavy machinery, Flynn Drilling decided to invest in bringing that work in-house.
They added two full-time mechanics to their growing team, dedicated to maintaining and servicing company-owned equipment. This change led to safer equipment and consistent work quality since the in-house mechanics could be trained on the company’s industry-specific machines. It also lets them perform proactive maintenance on their machinery instead of reacting when something stops working – saving time and increasing productivity.
“Drill rigs are complex, and specific knowledge is required to maintain them properly,” said Harke. “When we hired our own mechanics, the rest of the employees immediately started commenting on the change. They’re very happy with it.”
The next 25 years of safety
In a high-risk industry, Flynn Drilling breaks the mold by fostering a proactive, safety-first culture. It’s clear that leadership treats the company’s employees as their most important asset. “It’s about more than OSHA compliance here,” Harke remarked. “We encourage every employee to go above and beyond compliance to truly put safety first.”
MEM is celebrating 25 years of helping Missouri businesses build safer workplaces! Learn more. >